Plumbing is the system of pipes and fixtures installed in a building for the distribution of potable (drinking) water and the removal of waterborne wastes.
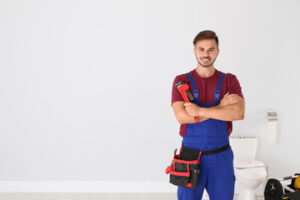
Plumbers repair and install pipes, fixtures, and appliances such as sinks and toilets. They also perform backflow testing for commercial and industrial properties.
Backflow occurs when water flows in the opposite direction than it’s supposed to. This can be dangerous, especially if your backflow prevention device isn’t working properly. Fortunately, there are ways to prevent this from happening.
Backflow prevention devices are essential for protecting the integrity of your plumbing system and your family’s health. These devices are designed to stop contaminants from entering your home’s water supply in the event of a backward flow. They work by incorporating one-way valves into your home’s plumbing. These devices only allow the municipal water supply to travel in one direction, but they close when that flow reverses. This keeps dirty water from contaminating your clean drinking water, such as from your toilets or drains. It also helps prevent sprinklers and garden hoses from transporting chemical fertilizers into your house’s water system.
There are many different types of backflow prevention devices and assemblies, ranging in complexity and cost. The type of backflow prevention device you need will depend on the level of risk in your household. For example, an air gap is a simple, inexpensive solution for low-hazard situations, while an RPZ assembly can protect high-hazard systems like those used in hospitals or industrial facilities.
In some cases, your local water authority may require you to install a backflow prevention device. This is especially true if your home is connected to the public water supply. If you’re required to install a backflow prevention device, it’s important to have it tested on a regular basis to make sure it is working properly.
The most common backflow prevention method is an air gap. This is a simple solution that works well in low-hazard situations, such as a hose bib or residential fixtures. Another option is an RPZ assembly, which is a mechanical backflow prevention device that uses sensors to detect changes in water pressure. These devices are typically installed in commercial and industrial buildings, and they can be expensive.
If your backflow prevention device isn’t functioning properly, it may be due to a blockage in the air gap or a leak in the gate valve. It’s important to have these issues fixed right away, as backflow can cause serious contamination and illness. You can find out if you have a backflow issue by having your device tested on a regular basis by a licensed plumber.
Check Valve
A check valve, also known as a non-return valve or foot valve is used to prevent backflow in piping systems. These simple devices are vital in keeping equipment safe and preventing costly reverse flow that can cause severe damage to pipes and pumps.
Generally speaking, check valves are inexpensive, easy to install and work well in a variety of applications and working conditions. They’re a crucial component in making sure equipment remains safe and functional and that reverse flow doesn’t cause the kind of catastrophic damage that can halt production or even severely harm workers.
There are several different kinds of check valves in use today. Most are based on the same principle of having a disc that is stabilized against an internal stop and only allows forward flow. The most common types of check valves are swing check valves, axial or rubber duckbill check valves, and ball check valves.
Swing check valves rely on a swinging cone or ball on the interior of the disc to seal against backflow. The spring in the valve helps to force the cone or ball onto its seat and opens when fluid is flowing through the system. If the system pressure decreases or the direction of flow changes then the spring is no longer able to help the valve to open and the valve will begin to close.
A axial or rubber duckbill check valve has a similar design with a flapper that is attached to one side and can only be opened when the system is flowing in the correct direction. This type of check valve is typically more resilient against backflow than swing valves and can be used in either horizontal or vertical installation, unlike swing check valves which are only capable of working in one orientation.
Ball check valves utilize a heavy ball to close the valve in most models, while some smaller inline versions of this type of check valve don’t use a ball at all and instead rely on gravity to keep the valve closed. Flow control valves can be added to these models to allow for greater control of the flow of liquid and gas through the check valve. These valves can be used in a wide variety of industrial applications including chemical feed pumps, boilers, pressure pumps and steam lines.
Gate Valve
A gate valve is a type of stopper in a pipeline that can block the flow. It differs from ball, plug and butterfly valve segments in that its closure element rises on the base of a stem out of the waterway, similar to how a gate closes over a castle’s door.
Gate valves can be opened and closed manually or by using an actuator. They can also be automatically operated to save time and effort. They are available in a wide range of materials and pressure classes. They can be made from castings, forgings or weld-fabricated assemblies, though casting designs are most popular. Their sizes range from fit-in-your-hand NPS 1/2 inch, all the way up to big-as-a-truck NPS 144 inch.
The trim of a gate valve contains the functioning pieces that allow the valve to open and close: the stem, the disc or wedge, and the seat rings. The seat rings prevent the wedge from moving away from the valve seat when opening or closing. The seat rings come in two varieties: metal or resilient (rubber) seated. The former is more durable and better able to resist corrosion, but the latter may trap solids that could be in the fluid.
While the rising stem and non-rising stem types have long been the most popular gate valve styles for industrial applications, the NRS is gaining favor in plumbing markets due to its cost effectiveness and ease of installation. The stem in a NRS is threaded into the disc, allowing the disc to rotate in conjunction with the handwheel to open and close the valve.
A flanged body connects the valve to the pipe. These bodies can be connected to the pipes through butt, socket or wafer end connections. The valve seat is sealed with gland packings. These packings are typically made of elastomeric materials and inserted into a box called a stuffing box.
While ball, plug and butterfly valve segments have been gaining market share in recent years, the gate valve segment remains strong and offers high value for the money. Understanding how they work, the different parts that make them unique and the specifications that should be considered when choosing a valve are vital to ensuring backflow prevention system safety and functionality. For more information about selecting the right valve for your home, speak to a local backflow professional today.
Pressure Gauge
The pressure gauge is one of the most important instruments in any backflow prevention device. It is a mechanical gauge that measures and indicates the system’s pressure through a dial or digital readout. There are many different types of pressure gauges, ranging from simple ones to more complex and costly industrial units. The type of gauge you choose depends on your needs and the environment where the unit will be used.
The most common type of pressure gauge is a Bourdon tube one, which is based on the operating principle that the deflection of a bellows (or a diaphragm in some cases) is proportional to the change in pressure and can be translated to a mechanical movement of a pointer or other indicator. Bourdon tube gauges are available in a wide range of sizes and accuracy ratings, and can be made from a variety of materials, including brass, stainless steel or monel (a nickel alloy).
A more sophisticated form of pressure gauge uses the Pirani gauge principle to measure gas pressure. This is based on the thermal conductivity of the metal wire that is heated or cooled in response to changes in pressure. A temperature sensor is attached to the gauge so that it can determine the actual temperature of the metal and calculate the pressure based on its temperature.
Other gauges are based on the operating principles of a piston or diaphragm and use magnetic fields to convert their motion into a readout. A magnet in the gauge case attracts a second magnet in the piston or diaphragm, which moves as the differential pressure increases and tugs at a rotary magnet that in turn moves a pointer on a dial or digital display. Some gauges also have internal stops that prevent the traveling parts from moving too far when excessive pressure is applied.
All mechanical pressure gauges must be carefully maintained to ensure their performance and longevity. The most common causes of failure are dirt and corrosion. This can be injected from the test cocks during backflow testing or it may occur due to the material of the gauge case itself, which can corrode and leave particles that restrict the element’s movement. It is important to flush the test cocks during backflow testing and pressurize the test kit slowly so that the pressure spike does not damage or inject debris into the critical moving areas of the gauge.